Design Procedure
Table of Contents
- 2. Chapter 2 of 3. DESIGN PROCEDURE
- 2.1 General
- 2.2 Site Investigation
- 2.3 Culvert Location
- 2.4 Operating Conditions
- 2.5 Headwater Levels
- 2.6 Losses
- 2.7 Ground Conditions
- 2.8 Culvert Sizing
- 2.10 Self-Cleaning Velocity
- 2.11 Outlet Velocity
- 2.12 Determining Culvert Invert Levels
- 2.13 Cover
- 2.14 Culvert Settlement
- 2.15 Culvert Length
- 2.16 Concrete Culverts
- 2.17 Culvert Floatation and Anchorage
- 2.18 Levees & Table Drain blocks
- 2.19 Outlet Drains
- 2.20 Culvert Schedule
- 2.21 Documentation
- References
2. Chapter 2 of 3. Design Procedure
2.1 General
The design of culverts should be carried out in accordance with Chapter 7 of Austroads Waterway Design Guide and Main Roads Standard Culvert Drawings.Some culvert sites may require a specialised Waterway Investigation Survey and this should be carried out in accordance with Main Roads Guide to Specialised Survey Applications.
2.2 Site Investigation
Gathering of information is important during site investigation. The items below represent the information that can be obtained from the site:- Scour and outlet protection at similar culverts in the vicinity (this will provide valuable guidance for design of outlet protection)
- Estimate of stream velocity, slope, and alignment. This information can also be used to verify design flows. Refer to Main Roads' Guide to Obtaining Design Flows
- Presence of shrubs and trees on eroding banks
- Watershed land uses, particularly logging, cultivation, and construction
- Soil characteristics
- Manning's roughness coefficient
- Storage of debris and materials within the flood plain (logs, lumber, solid waste, etc) as this material could govern the minimum size of culvert to be used.
- Anecdotal information on the performance of any existing drainage
2.3 Culvert Location
Culverts should be provided for all natural watercourses and drains intercepted by the road. In some catchments it may be desirable to concentrate the flow into one crossing by using longitudinal drains ('B' drains) to reduce the number of road crossings.
Careful selection of the culvert alignment, grading and size will achieve good hydraulic performance, stability of the stream bed, reduce risks for errant vehicles, and will minimise construction and maintenance costs. It is important to design the culvert to be free from sediment deposits, which tend to occur on the inside of stream bends, or where there is an abrupt change from the stream slope to a flatter grade in the culvert.
A culvert should be laid on a straight alignment, which may be either perpendicular or skewed to the road centreline.
The Designer should not introduce severe changes in channel alignment and in particular the construction of short radius bends in the channel as they are likely to erode on the concave bank, and to build up sediment on the opposite bank. To avoid this it may be preferable for the Designer to place a culvert on a skew.
Acceptable skew angles of culverts varies from 0degrees to a maximum of 45degrees. The upper limit is dictated by the inefficient end treatment of the culvert structure in transitioning the flow from the stream into the culvert.
Main Roads Standard culvert drawings show skewed culverts with the wingwalls on a skew but the headwall parallel to the road centerline to maintain a constant offset from road centerline to the culvert headwall.
2.4 Operating Conditions
As shown on Figure 2.1 and 2.2, two flow conditions are possible in culvert flow and they are referred to as inlet control and outlet control flow conditions. Inlet control refers to the situation where the capacity of the culvert is entirely influenced by inlet factors such as the width of the inlet and approach conditions. The water surface profile within the culvert approaches the normal depth profile and the culvert behaves as an open channel.
Outlet control refers to the situation where a combination of the culvert size, roughness and tailwater conditions influence the discharge capacity of culvert. The flow conditions are similar to pressurised pipe under full flow condition.
In the design process, the headwaters corresponding to both inlet control (HWi) and outlet control (HWo) situations need to be analysed. The higher of the two values defines the flow condition, i.e. inlet control is deemed to be the flow condition when HWi is higher than HWo and vice versa.
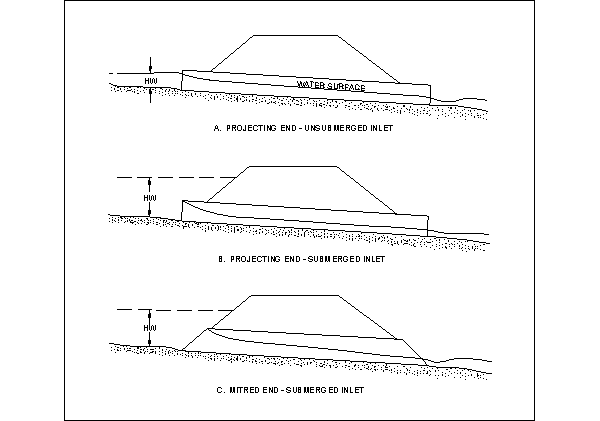
Figure 2.1 Flow Profiles for Culvert Under Inlet Control (AUSTROADS,1994) |
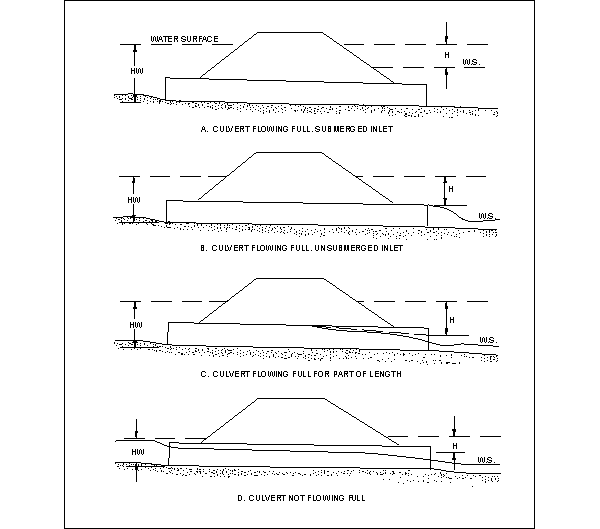
Figure 2.2 Flow Profiles for Culvert Under Outlet Control (AUSTROADS,1994) |
For details on culvert operating conditions refer to Section 7.3 of Austroads Waterway Design Guide (1994).
2.5 Headwater Levels
The maximum allowable headwater is limited by factors such as:- possible property damage to upstream properties due to flooding;
- potential hazard to persons or stock due to depth of water;
- damage to the culvert or the roadway;
- interruption of traffic;
- damaging effects of water infiltrating the pavement;
- overtopping of the road and subsequent damage.
In instances where the headwater level remains at the top of road subgrade level or higher for periods longer than 24 hours the pavement should be designed using soaked CBR values for the subgrade.
2.6 Losses
2.6.1 Inlet, Outlet and Friction Losses
The head loss coefficient for a culvert exit (outlet) is often assigned a value of unity while head loss coefficients (ke) for different entry conditions are listed in Figure 7.17 Austroads Waterway Design Guide.
The friction loss varies with the barrel (cell) length and material of the culvert, and can be determined using the equation 7.4 of the Austroads Waterway Design Guide.
2.6.2 Inlet Losses in Multi Barrel Culverts
For multiple barrel culverts acting under inlet control the turbulence at the entry to one barrel can affect neighbouring barrels (or cells) and exacerbate the losses. This will result in higher losses than normally being computed for a single barrel culvert.
These losses can reduce the capacity of the culverts by 30% and as high as 70%. When designing multi-barrel culverts the Designer should undertake some sensitivity analysis to determine what effect this reduced capacity will have. If the reduced capacity will significantly increase the headwater in a susceptible area for the design event or cause excessive damage to the road pavement then the Designer should increase the capacity of the culverts to cater for these additional losses.
2.7 Ground Conditions
The existing ground conditions at drainage locations must be assessed as "Aggressive" or "Non Aggressive" for the purpose of selection of the appropriate cover to the reinforcement in precast concrete culvert and pipe units. The aggressive environments include the following conditions:- Arid regions with salt rich soils
- Regions such as the Wheatbelt which produce saline flow
- Tidal or splash zones
- Sites where the drainage conduit is exposed to prolonged wetting and drying
- Permeable soils with a pH < 4.0
- Ground water containing more than 1 g per litre of sulphate ions.
Main Roads does not allow use of standard (galvanised) corrugated steel culverts in the areas with aggressive ground conditions, but does permit the use of approved polymer-coated corrugated steel pipe culverts in these conditions.
2.8 Culvert Sizing
Various computer programmes are readily available for the hydraulic design of culverts.The design Nomographs provided in Chapter 7 of the Austroads Waterway Design Guide can be used.
A range of Manning's n for concrete pipe culverts, concrete box culverts and corrugated steel (pipe and arch) culverts are as specified in Table 2.1 and Table 2.2.
Type of Culvert |
Roughness or |
Manning's n |
Concrete Pipe (RCP) |
Smooth |
0.011-0.013 |
Concrete Boxes (RCB) |
Smooth |
0.012-0.015 |
Corrugated Steel |
150 by 50mm |
0.033-0.035
|
Table 2.1 Manning's n value for RCP, RCB, and Corrugated Steel Arches (Source NHI; 2001)
Diameter (mm)
|
Manning's Coefficient (n) |
||
Corrugations - Pitch X Depth (mmxmm) |
|||
|
68X13 |
75X25 |
125X25 |
300 |
0.011 |
# |
# |
375 |
0.012 |
# |
|
# |
|||
450 |
0.013 |
# |
# |
600 |
0.015 |
# |
# |
750 |
0.017 |
# |
# |
900 |
0.018 |
0.022 |
# |
1050 |
0.019 |
0.022 |
# |
1200 |
0.020 |
0.023 |
0.022 |
1350 |
0.021 |
0.023 |
0.022 |
1500 |
0.021 |
0.024 |
0.023 |
1650 |
0.021 |
0.025 |
0.024 |
1800 |
0.021 |
0.026 |
0.024 |
1950 & Larger |
0.021 |
0.027 |
0.025 |
Table 2.2 Manning's n value for Helically Wound Corrugated Steel Pipes (Source: AISI; 1999)
Note: # Indicates that no pipes are available in this pitch x depth.
2.10 Self-Cleaning Velocity
The self-cleaning velocities of culverts are dependent on a variety of factors such as soil grain size, duration of flow and frequency of flow. It is desirable to maintain a self-cleaning velocity in the culverts to prevent deposit of sediments and subsequent loss of capacity. For this reason, culverts should be generally designed to maintain velocities of 0.7 m/s for loose clay soil and about 0.9m/s for the soils with a larger grain sizes.2.11 Outlet Velocity
Culverts usually result in outlet velocities which are higher than the natural stream velocities. These outlet velocities may require energy dissipation to prevent down stream erosion. Main Roads generally uses rock protection to prevent down stream erosion. If required, rock protection shall be designed for the same ARI as the culvert design.Where the culvert is subject to velocities in excess of 3 m/s, the apron must be designed to extend beyond the hydraulic jump lengths. Where the velocities are 3 m/s at the edge of the exit apron rock protection works are necessary.
Rock protection should be in accordance with Table 6.1 of the Austroads Waterway Design Guide.
2.12 Determining Culvert Invert Levels
Culvert invert levels should be set to :- Satisfy cover requirements as specified in Section 2.13.
- Prevent ponding on the upstream and downstream sides.
- Prevent protrusion of culvert sections, including link slabs into the pavement layer. If this criterion cannot be met the road formation level and/or culvert invert level and/or the culvert size should be adjusted.
- Ensure that excessive lengths of outlet drains are avoided by locating invert levels at natural streambed levels.
As a part of the design process the culvert inverts should be pegged on site as a check to ensure that the culverts are located correctly and at the right levels.
2.13 Cover
The term cover describes the distance from the top of the pavement to the top of the culvert barrel. Required cover shall be provided across the pavement through to the edge of the shoulder.The minimum depth of cover required for a pipe culvert is a function of the pipe type (e.g. concrete or steel), dead and live loading and in the case of concrete pipes the class of pipe. When determining the cover, the distance from the finished road surface to the crown of pipe collar should be used.
The minimum cover required for box culverts should be determined in accordance with Main Roads Standard Culvert Drawings and the product catalogues.
The construction loadings during construction should be considered when determining cover requirements for culverts. Where heavy construction equipment is used, greater cover may be required. This can be achieved by either placing the culvert barrel deeper, or by placing temporary fill above the culvert barrel during construction.
The cover requirements for various culvert types are described below.
2.13.1 Box Culverts
As shown on Main Roads Standard Box Culvert Drawings (Drawing No. 9530-1291) the minimum cover on box culverts is 0.5m to finished surface level. In the cases where this criterion cannot be met the culvert base slab shall be redesigned.
Generally the maximum cover for the commercially available box culvert crown units are 4.5m. This should be checked and confirmed with the manufacturers if boxes are to be used under fills of this height or greater.
2.13.2 Reinforced Concrete Pipes (RCP)
The minimum cover should be in accordance with the Concrete Pipe Association's Concrete Pipe Selection and Installation Guide.
For heights of fill which warrant the use of a concrete cradle (Type H3 support in accordance with AS 3725 Loads on Buried Concrete Pipes: 2001), it is often preferable to use pipes of a higher cracking load than Class 4. The economic limit of these pipes is usually Class 8 to Class 10 depending on the site location and conditions. The hydraulic performance of pipes over Class 4 is reduced, due to the reduced internal pipe diameter. Also for pipes over Class 4 the advantage of a higher Class pipe can be reduced due to extra wall thickness cast outside the pipe collar (reduced cover).
2.13.3 Corrugated Steel Pipes
The minimum cover to corrugated metal pipes should be determined in accordance with AS 1762 Helical Lock-Seam Corrugated Steel Pipes Design and Installation 1984, and AS/NZS 2041 Buried Corrugated Metal Structures: 1998. Maximum height of fill may vary from 10 metres to 50 metres, depending on the site loading conditions and the structural strength of the pipe. Minimum cover for the Helical Lock-Seam Corrugated Steel Pipes are:
- Minimum Cover for Railway Live Loads - Ss/4 or 1.0m, whichever is greater
- Minimum Cover for Highway Live Loads - Ss/6 or 0.6m whichever is greater
2.13.4 Corrugated Aluminium Pipes
Corrugated aluminium pipes have been used in the past by various Main Roads' Regional offices. Although the use of aluminium pipes is not common now, if aluminium pipes are required the structural design procedure shall be based on AS 1762, modified to suit aluminium properties of Alclad Alloy 3004-H34 (defined in AS/NZS 1734:1997) with regards to metal strengths and flexibility.
2.14 Culvert Settlement
Where culverts are liable to settle due to a compressible subgrade or a high fill, measures should be taken to ensure that the pipe assumes the design grading after settlement has occurred.In broad terms, the Designer should consider:
- the grade and capacity of the pipe prior to settlement;
- a generous longitudinal grade if substantial settlement is expected;
- selection of pipe types which can remain serviceable under the anticipated settlement, for example, corrugated steel pipes or rubber ring jointed pipes;
- initial deferment of endwalls, as these may be damaged during settlement.
2.15 Culvert Length
The length of culverts shall be determined following assessment of the road cross-section at the proposed culvert site.The Designer should obtain a cross section at the proposed culvert location to determine the required length of culvert and the headwall height. The fill batter slope shall be retained (i.e not locally steepened) and the culvert length shall be in multiples of current industry product lengths. The Designer shall include the unit lengths used in determination of the culvert lengths on the culvert schedule drawing (Drawing No. 200331-0044).
As shown on Main Roads Standard Drawing (Drawing No. 200131-0061) for RCP's the headwall height measured from the obvert, can vary from a minimum 300mm to a maximum of 600mm. For the box culverts (Drawing No. 0130-2875) the maximum height of headwall is 500mm. Culverts requiring a headwall height over the above upper limits shall be designed individually.
Culvert length, apron lengths and headwall height must be designed to suit the embankment batter at the culvert site. It is ideal to locate the culvert headwall outside the clear zone (as specified in AASHTO Roadside Design Guide Table 3.1) whenever it is possible. When this criterion cannot be met, the headwall shall be located either outside the pavement batter or at an absolute minimum of 1.0m from the edge of finished shoulder whichever is greater. The top surface of headwall must not project above the finished batter level. Headwall faces must generally be parallel to the road shoulder.
Some culverts (depending on the size of the culvert) may require the installation of a safety barrier. The requirement for a safety barrier should be determined in accordance with Main Roads Guide to Safety Barriers.
2.16 Concrete Culverts
Concrete drainage pipes must be commercially available pipe sections, manufactured in accordance with Main Roads' Standard Specification 404 Culvert and Stormwater Drains.Box culverts and link slabs with spans less than 1200 mm and link slabs with spans 1500 mm and larger, must be manufactured in accordance with Main Roads' Standard Specification 404 Culvert and Stormwater Drains.
2.17 Culvert Floatation and Anchorage
Flexible barrel materials (eg CSP) are vulnerable to floatation because of their light weight and lack of resistance to longitudinal bending. Floatation is the term used to describe the failure of a culvert due to the uplift forces caused by buoyancy. The buoyant force is produced when the pressure outside the culvert is greater than the barrel. This occurs in a culvert acting in inlet control with a submerged upstream end. The phenomenon can also be caused by debris blocking the culvert end or damage to the inlet. The resulting uplift may cause outlet or inlet ends of the barrel to rise and bend. Occasionally, the uplift force is great enough to dislodge the embankment.
Large projecting or mitred corrugated steel pipe culverts are the most susceptible to floatation. In some instances, high entrance velocities will pull the unanchored inlet edges into the culvert barrel causing blockage and additional damage.
A number of precautions can be taken by the Designer to guard against floatation and damage due to high inlet velocities. These include:
- Protecting steep fill slopes against erosion as this helps inlet and outlet stability
- Avoiding the use of large skews under shallow fills
- Anchorage at the culvert ends. Anchorage is a means of increasing the dead load at the end of a culvert to protect against floatation. Concrete cutoff walls and head walls are common forms of anchorage. The culvert barrel end must be securely attached to the anchorage device to be effective. Provision of culvert anchorage also provides protection against inlet bending, inlet warping, and erosion to fill slopes. Refer Main Roads Standard CSP Culvert Drawings (Drawing Nos. 200131-0064, 200131-0065, 200131-0066) for more details.
2.18 Levees & Table Drain blocks
To generate the maximum headwater at the culvert it may be necessary to install a levee. If water is required to be forced into the culvert from the table drain then the Designer may need to consider installing table drain blocks.Typical details for levees, drain types and table drain blocks can be found on Main Roads Standard Drawing No. 9831-5498.
2.19 Outlet Drains
Where inlet or outlet levels are below existing surface levels a drain (typically 'F' drain) is required. The required length of F drain is determined by "daylighting" the drain, i.e. constructing a drain until its reaches the natural surface. Typical 'F' drain details can be found on Main Roads Standard Drawing No. 9831-5498.
2.20 Culvert Schedule
A culvert schedule is required to specify details of each culvert. The culvert schedule should contain the information shown on the Main Roads Drawing No. 200331-0044.During the preliminary design phase of a project the culvert schedule can be provided in the form of a spreadsheet but should include a note on what multiple lengths or units has been used as the basis of the design.
Main Roads' generally use three different end treatments for CSP culverts, with endwalls, cut-ends and uncut-ends. CSP culverts with cut-ends are to be cut in accordance with Drawing No. 200131-0066 also refer to 200131-0065 for details of endwall. Therefore it is necessary to provide end treatment details for each culvert on the culvert schedule. A typical example for the detail required is as follows:
C.S.P. |
|||
PIPE |
NUMBER |
CUT ENDS |
|
SQUARE |
BEVELLED |
Where there are existing culverts to be removed then these can also be shown in the culvert schedule. The Chainage and size of the culvert should be included in the culvert schedule with the comment "REMOVE" in the column labelled Remarks. Refer to Culvert Schedule Drawing No. 200331-0044 for more details.
2.21 Documentation
The following information shall accompany the culvert design:- Basis for the calculation of the flows
- Design recurrence interval both for the culvert and scour protection
- Outlet velocity
- Condition culvert is expected to operate under e.g. inlet or outlet control
- Maximum headwater value used for the culvert
- Any assumptions used in sizing of the culvert
- Method used for calculating culvert size e.g. nomograph, computer program etc
- Culvert cross sections indicating road reference line and offsets to headwalls (these can be hand drawn)
- Culvert schedule (Refer to Section 2.20)
- Pipe bedding (Refer to Chapter 3)
- Degree of pipe support assumed in determining pipe class (if concrete) or wall thickness for steel culverts (Refer to Chapter 3)
- Observations made during site visits which have been used to determine or justify extent or lack of outlet protection
- Installation condition (Refer to Chapter 3).
References
AUSTROADS, Waterway Design, A Guide to the Hydraulic Design of Bridges, Culverts and Floodways (1994).
National Highway Institute (NHI); Federal Highway Administration, Hydraulic Design of Highway Culverts; Hydraulic Design Series Nimber 5; (2001).
American Iron and Steel Institute (AISI), Modern Sewer Design, (1999).
AS/NZS 2041 Buried Corrugated Metal Structures, (1998).
AS/NZS 1734 Aluminium and Aluminium Alloys - Flat Sheet, Coiled Sheet and Plate, (1997)
AS/NZS 1762 Helical Lock-Seam Corrugated Steel Pipes Design and Installation, (1984).
AS/NZS 3600, Concrete Structures; (2001).