The Beam Team on BORR Pours the Last Precast Mould
The Bunbury Outer Ring Road (BORR) project has reached a significant construction milestone, or should we say mouldstone, with the final of 153 precast bridge beams being moulded onsite at our fabrication centre in Picton.
Published: 29 February 2024, Updated: 29 February 2024
After 15 months of work, the final precast beam mould has been poured at the local fabrication facility for the BORR project. Precast beams are bridge beams created offsite and then transported to site ready for installation.
The first pour took place in November 2022 and the 153rd (and last) took place last month in January 2024.
Why do we use precast beams?
Precast beams offer several important benefits for a project like the Bunbury Outer Ring Road.
They provide greater efficiency in the beam creation/installation process resulting in speedier construction times. Using precast beams means the team also has greater quality control in ensuring the beams are fit for purpose and made to specification for the respective bridge’s needs. Commercially, precast beams result in greater cost efficiency with fewer unexpected delays and transport logistics required.
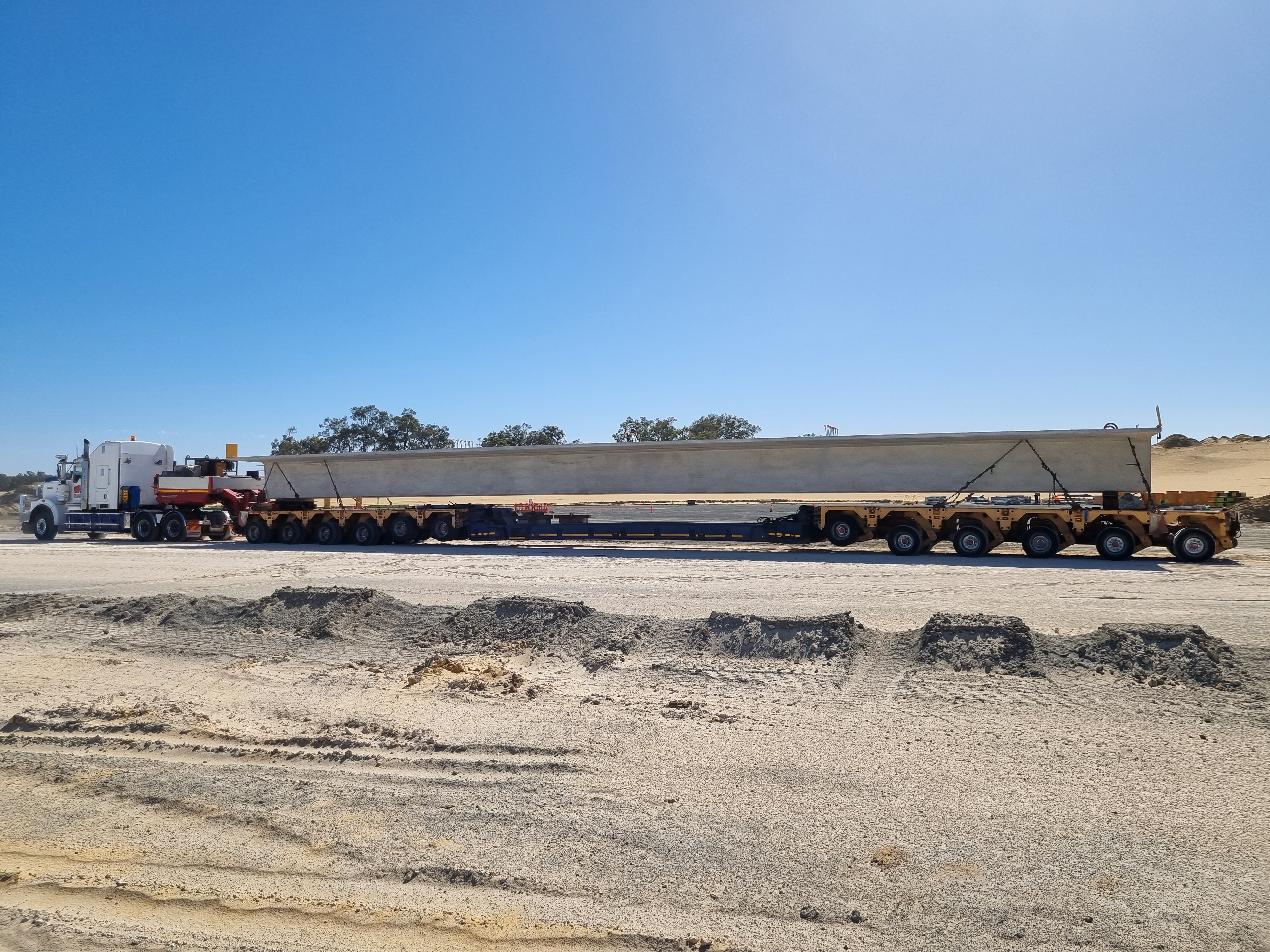
A beem being transported to site
How long did it take?
The 153 precast tee-roff beams were poured over the course of 434 days in total and required approximately 82,000 hours of combined labour by the team. To get the job done, we operated a 24-hour, six-days-a-week workforce roster.
In addition to carrying out the beam pours themselves, the team had to ensure every beam met the highest of standards and specifications needed for the bridges on BORR.
The graph below details the number of beams that were cast and moulded each month since November 2022.
How much concrete was used?
Across all 153 tee-roff beams, 102 individual concrete pours were conducted using a grand total of 8,000m3 of concrete i.e., well over two Olympic swimming pools’ worth of concrete.
Three distinct mould depth profiles were required for the bridge designs, allowing us to fabricate beams ranging from 21 metres to as long as 44 metres in length. The above ground mould and stressing system itself was 68 metres in length to facilitate beams of these sizes.
To meet production specification and durability requirements, a water heating and cooling system was incorporated in the mould which was capable of controlling beam concrete temperature.
What happens to the beams after being poured?
Once each bridge beam is poured, our pair of 110-tonne capacity straddle carriers—heavy duty vehicles used for lifting and transporting large and heavy loads—were brought in to seamlessly lift the precast beams out of the moulds and load them onto trucks for transportation to site.
With all beams now fabricated, it is time to continue putting them into place on the various bridges along the BORR alignment.